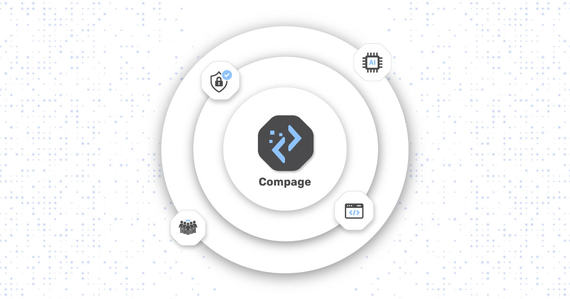
Introducing Compage – Dev-Centric Platform for Auto-Code Generation & Fortified Security
Organizations today face a slew of challenges that significantly impact their growth. According to a survey …
Industry 4.0 has swept through the manufacturing industry, with manufacturing technology companies finding ways to innovate to boost cost and production efficiency. However, this has opened doors to new challenges that impact supplier relations, production processes, customer satisfaction, and quality control. Each technological leap presents hurdles for manufacturers seeking sustainable growth. The answer lies in industrial modernization - the act of adapting and updating manufacturing practices.
Manufacturers, burdened by legacy data systems (spreadsheets, ERP, and MES platforms), fear Industry 4.0 as another rigid layer. The prospect of significant financial investments and resource allocation towards setting up new tools and the perpetual task of coordination and bridging data gaps looms large.
Integrating modern technology into manufacturing workflows presents a critical challenge; legacy systems resist collaboration. This mismatch impedes information flow and cross-functional cooperation, hindering efficiency and agility.
Disconnected Teams: Separate workflows and systems across departments and plants create information barriers. This impedes timely communication and coordinated decision-making, especially during urgent situations. Managers lack a holistic view and struggle to respond swiftly to production hiccups that could snowball across the system.
IT/OT Divide: Compounding the siloed operations issue is the widening IT/OT divide. Aging legacy infrastructure and applications across disparate on/off-premises technology stacks create significant “technical debt.” This complexity burdens new projects, hindering agility, productivity, and ROI. Proprietary technology standards and high switching costs associated with legacy systems restrict flexibility and vendor choice, further exacerbating vendor lock-in risks.
Industry 4.0 means machines, devices, and systems communicate effortlessly within the factory setting. This interconnected network facilitates real-time data exchange, enabling a more agile and responsive production process.
Leveraging performance monitoring, data analytics, and connected CMMS software, manufacturers can execute preventive and predictive maintenance strategies effectively. By identifying potential equipment malfunctions, companies can proactively schedule corrective measures, minimizing downtime and ensuring smooth operations.
Reduced human error, enhanced visibility, and real-time monitoring translate into expedited product development cycles. With digitization enabling greater resource allocation towards high-value activities and process optimization, manufacturers can swiftly bring innovations to market, gaining a competitive edge in the industry.
With transparency and insight into every facet of their operations, businesses can analyze performance metrics and address areas requiring improvement or optimization, driving organizational efficiency and innovation.
Industry 4.0’s automation surge drives real-time visibility and streamlines workflows across entire enterprises. Beyond shop floor operations, workflow automation and process management platforms, with their advanced functionality, security, and integration, are gaining traction as organizations seek to optimize all processes, offering a clear advantage over traditional ERPs.
There is an imperative in manufacturing to modernize IT infrastructure and adopt new paradigms like cloud-native technologies. This shift away from siloed, legacy systems towards an application-driven, integrated architecture unlocks hidden potential, and DevSecOps stands at the forefront of this transformation.
By integrating DevSecOps principles across the manufacturing pipeline, from supply chain management to quality control and customer service, businesses can reap significant benefits. Automation replaces manual, error-prone processes, minimizing defects and enhancing product quality. Security becomes an embedded feature, not an afterthought, as DevSecOps workflows weave safeguards into the development cycle.
But the impact goes beyond immediate gains. DevSecOps fosters a culture of collaboration, breaking down departmental silos and encouraging cross-functional teams. This exchange of knowledge, best practices, and feedback fuels continuous improvement, problem-solving, and streamlining operations. Moreover, the iterative nature of DevSecOps facilitates rapid innovation, enabling manufacturers to adapt to market demands and technological advancements swiftly.
While outdated systems might seem convenient to work with, they ultimately fail to adapt to evolving customer needs. However, modernization, despite being crucial, isn’t smooth sailing either:
Modern applications built with microservices and Kubernetes empower manufacturers with both increased innovation and streamlined operations. However, harnessing this potential requires rapid modernization using cloud-native solutions.
Compage bridges this gap. This agile app modernization platform automates code generation via its language-agnostic framework, integrates with diverse technologies seamlessly, and simplifies validation and adoption. Swiftly adapt to market shifts, build unified systems, and gain real-time insights for streamlined operations. Deliver superior experiences within your plant and beyond. Modernize cost-effectively, build resilience, and thrive in the digital age – Compage is your go-to solution to conquer your modernization challenges.
Want to see Compage in action and how it benefits manufacturers? Drop us an email at hello@intelops.ai to schedule a demo. Check out all that we have been up to on LinkedIn!
Organizations today face a slew of challenges that significantly impact their growth. According to a survey …
The mortgage industry has experienced significant shifts within various facets of lending process as a result …
We recently launched a new open source project for cloud native ecosystem & first of its kind! Give us a …
Finding the right talent is pain. More so, keeping up with concepts, culture, technology and tools. We all have been there. Our AI-based automated solutions helps eliminate these issues, making your teams lives easy.
Contact Us